石墨烯、碳纳米管等碳基导热聚合物复合材料的散热性能
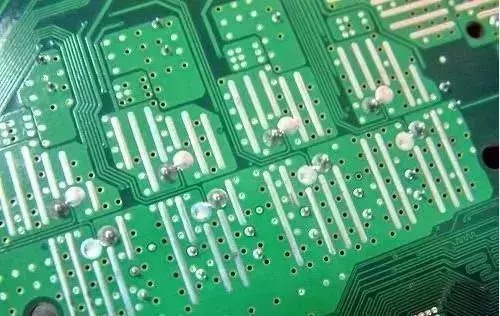
即使可以通过改变聚合物分子的规则性来增强聚合物的导热性,但是效果十分有限。在聚合物分子中加入导热填料形成聚合物网络是增强聚合物复合材料导热性最有效的方法。近年来,对各种类型的粒子做了全面的研究,它们的导热系数值见下表1.,根据使用要求,在需要绝缘体纳米复合材料时,广泛使用硅、硼碳酸盐、氮化硼、氧化铝等电绝缘填料。对于没有绝缘要求的应用,可以使用导电填料,如碳纳米管、石墨烯和金属纳米颗粒。
|
|
|
|
|
|
|
|
|
|
|
|
|
|
|
|
|
|
|
|
|
|
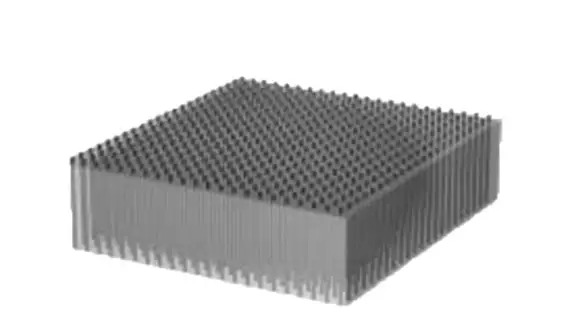
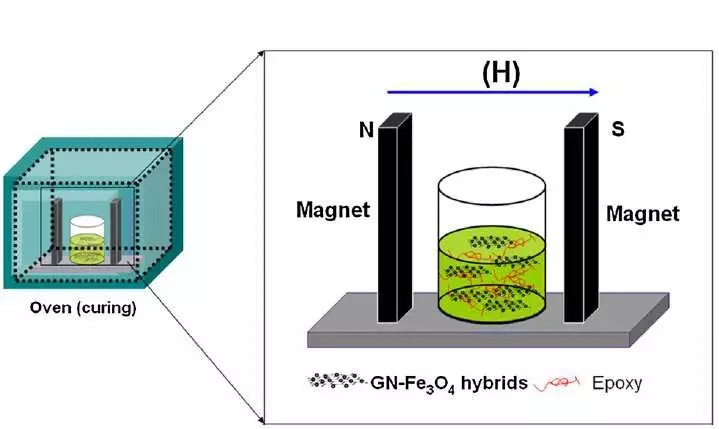
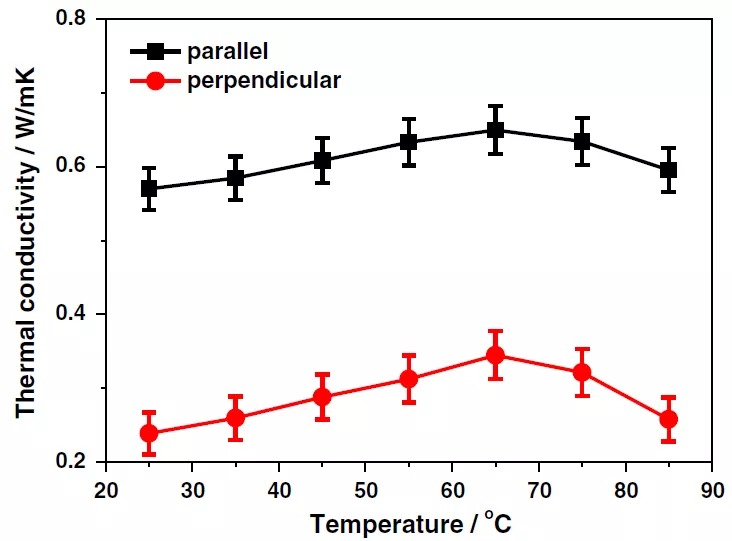
随着科学技术的飞速发展,对导热纳米材料提出了更高的要求。聚合物复合材料具有良好的导热性能,已广泛应用于生物电子、柔性电子、太阳能电池、换热器等领域。另一方面,导热系数较低的热电材料作为聚合物复合材料的首选材料,正成为新的研究热点。石墨烯、碳纳米管等碳材料具有导热性高、机械性能优越、成本低等优点,在开发高导热材料方面一直处于领先地位,已被广泛应用于制造导热聚合物复合材料。
参考文献:Yinhang Zhang, Young-Jung Heo, Yeong-Rae Son, Insik In, Kay-Hyeok An, Byung-Joo Kim, Soo-Jin Park
Recent advanced thermal interfacial materials: A review of conducting mechanisms
and parameters of carbon materials
https://doi.org/10.1016/j.carbon.2018.10.077